John Kennedy | 23 August, 2023
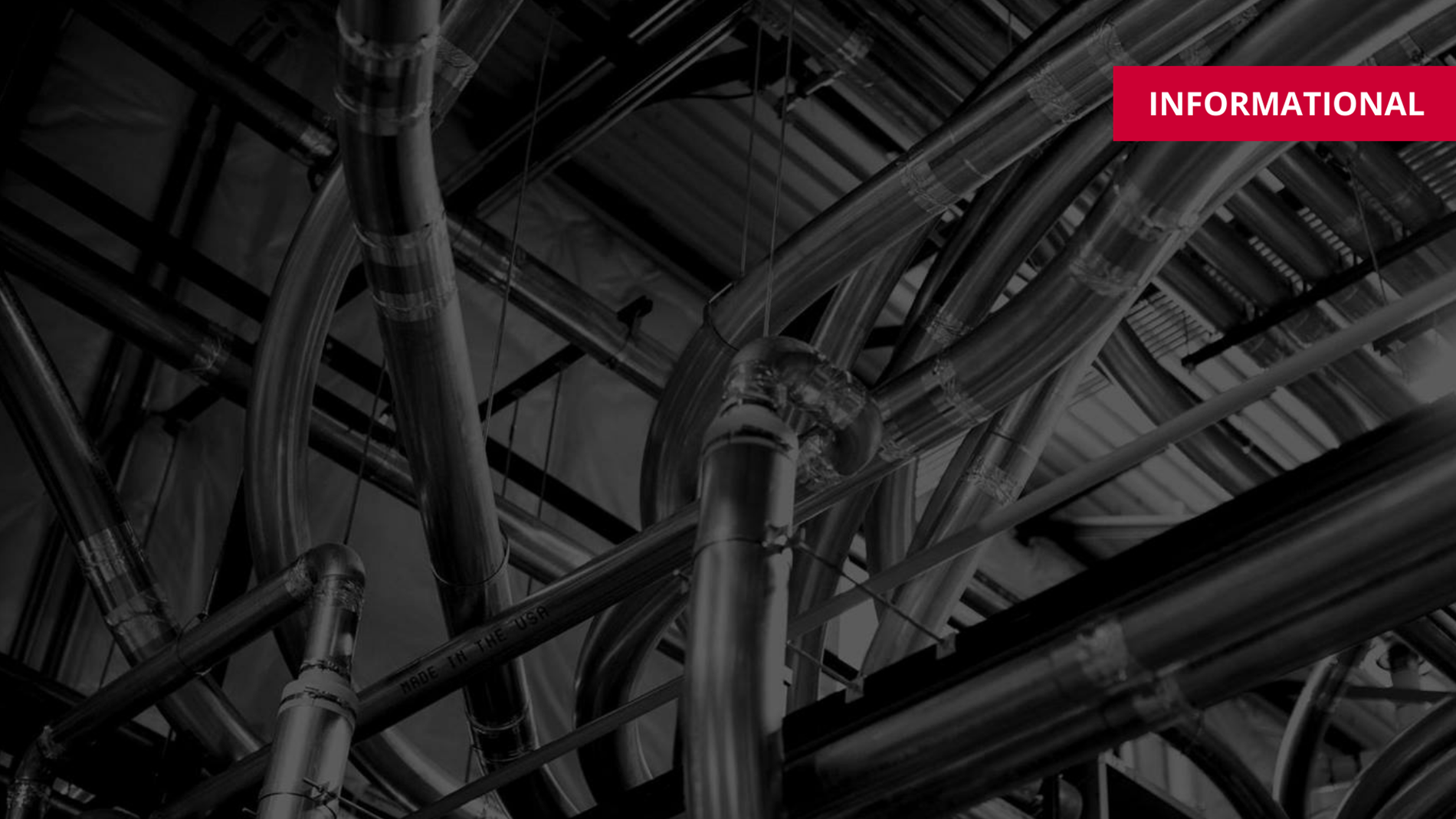
How a Pneumatic Tube System Works
A Closer Look at One of the Hospital's Most Critical Systems
A Brief Introduction to the Pneumatic Tube System
Pneumatic tube systems, more colloquially known as ‘tube systems’, act as critical transport infrastructure for many industries and institutions – including but not limited to warehouses, banks, mail centers, manufacturing facilities, hospitals, and pharmacies. However, as impressive as they are, the basic technology has been around for some time.
One of the earliest pneumatic tube systems can be traced as far back as the 1850s, when British engineer Josiah Latimer Clark started using vacuum operated tubes and cylindrical carriers to send mail between the London North-West District post office and Euston station in London.
Not long after, in 1869, Alfred Ely Beach spearheaded the construction of a large diameter tube system for the purpose of human transit in New York City, but the technology for this application failed to get the political and financial backing it needed to expand. However, its popularity in the mail room persisted.
In the 1950s, advances in plastics and other materials helped the tube systems become the delivery backbone of the hospital. As a result, caregiving staff could send oral solids (pills), paperwork, and x-rays quickly, safely, and efficiently. By the late 1970s and early 80s, tube system technology evolved to better accommodate the transport of sensitive items like lab specimens and blood products.
Today, pneumatic tube systems are even more advanced. Features like Radio Frequency Identification (RFID) tracking, software-controlled traffic management, and the ability to send multiple carriers at a time to different destinations means modern tube systems are sophisticated and ultra-efficient, but the principle by which they operate is still very much the same as it was in the mid-19th century.
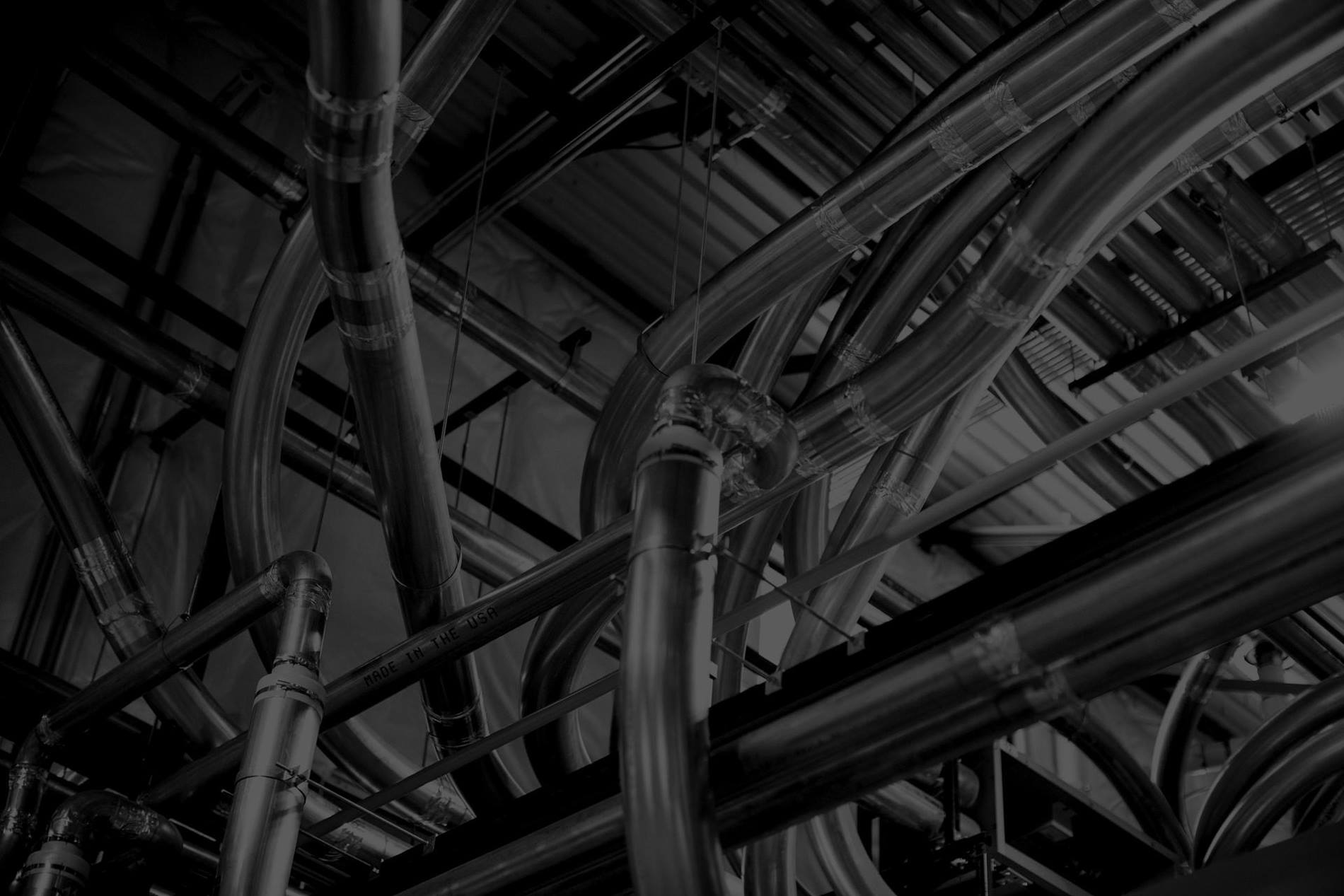
How a Pneumatic Tube System Actually Works
The way a pneumatic tube system works is simple but brilliant. A carrier, which possesses a special exterior band to create an airtight seal with the system piping, is inserted into a tube at a station. Once the carrier is secured inside the station, an industrial blower creates a vacuum in the tube on one side of the carrier or – depending on the intended direction of the delivery - pressurizes the tube on the opposite side.
The result? A carrier that can transport its contents upwards of 25 feet per second with exceptional control and efficiency.
The carrier then arrives at the intended station where the process can be repeated. To change the direction of the carrier, the tube system employs air valves that switch either vacuum or pressure to the system pipe.
Think of it like blowing a wet piece of paper through a straw or using a vacuum to move it through the straw in the opposite direction.

The Modern Pneumatic Tube System
As previously mentioned, tube systems have been around for over 170 years. In fact, TransLogic, a Swisslog Healthcare Company has been manufacturing and servicing pneumatic tube systems since the early 1900s, but much has changed since then. The tube systems of today are much more reliable, capable, and sophisticated from technological standpoint.
In addition to the basic principles of how a pneumatic tube system works, modern systems also make use of:
- Modern Materials – Durable and lightweight polymers make carriers light and strong. Carrier seals also last much longer due to advances in materials science.
- RFID – An alternative to barcoding, RFID carrier tracking ensures carriers are delivered to the correct destination. This is especially important in a hospital where drugs, specimens, and patient safety, are closely monitored. This is done by using a network of Radio Frequency Identification readers.
- Digital Stations – Digital touchscreen enabled stations allow for more complex sends e.g. putting five carriers into the station and sending them to five destinations simultaneously.
- Transfer Units – Commercial pneumatic tube systems are often comprised of a complex network of tube systems that can span thousands – if not tens of thousands - of feet. Transfer units are computer controlled pipe switches that connect the various tubes and allow carriers to transfer to different networks of tubes.
- Software – Modern tube systems are largely controlled and monitored by proprietary software that gives users, management, and maintenance staff the information they need to use, monitor, and maintain these systems.
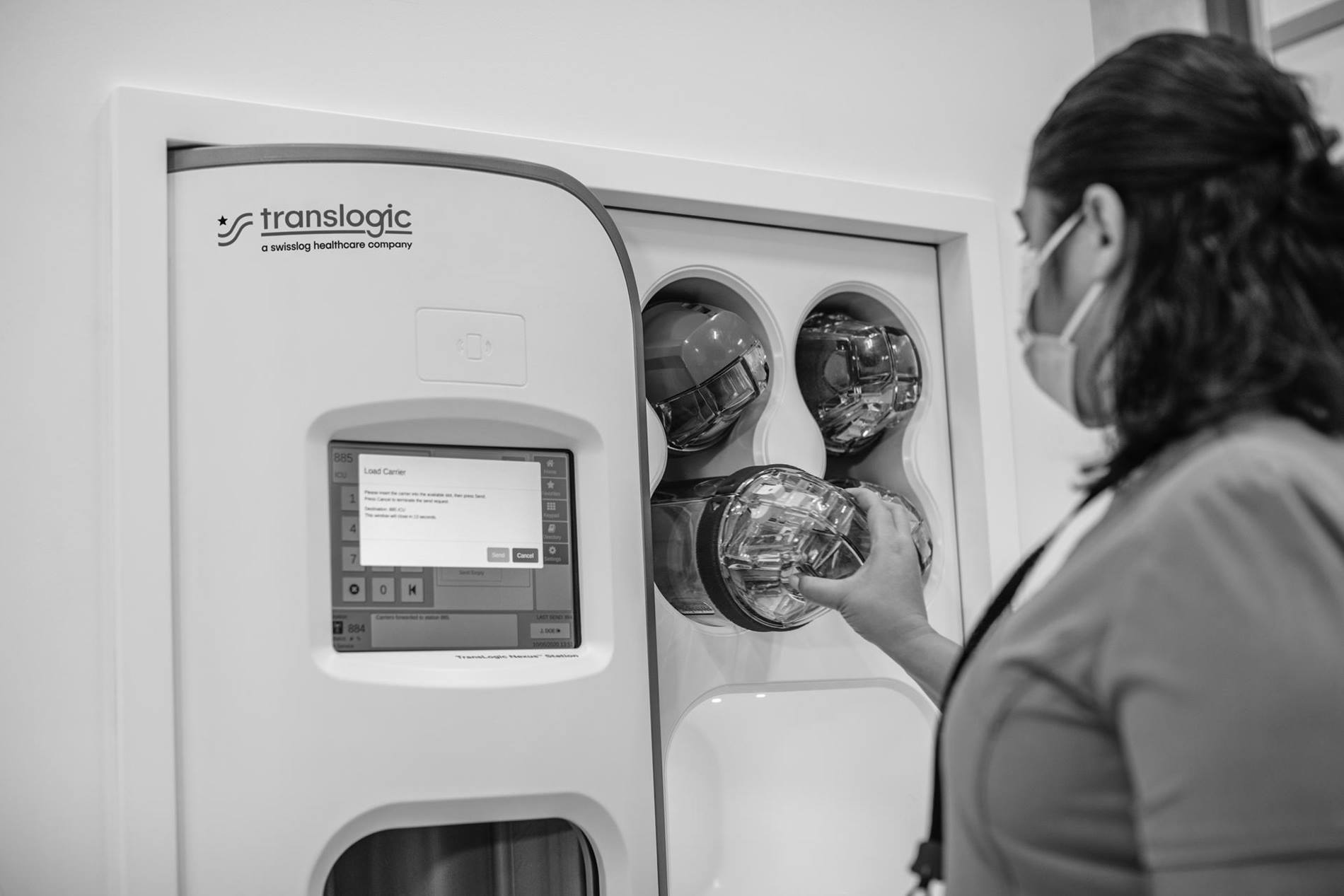
Benefits of a Pneumatic Tube System
The benefits of a pneumatic tube system have long been realized and include everything from enhanced safety and freeing-up staff, to centralizing operations with game-changing efficiency.
Today’s systems provide invaluable support for hospitals and other organizations, making thousands of transactions per day. They play a critical role in automating internal supply chains as well as creating efficiencies across departments by connecting investments in automations made elsewhere – an initiative that’s only poised to grow.
With a thoughtfully designed and installed tube system, not only do you create infrastructure that will serve the organization for many decades – the ROI is relatively short, making it a no-brainer.
For more information on how tube systems work or how they can help your organization, please reach out to your local TransLogic expert or try our ROI calculator to see for yourself.